Keywords: high frequency quenching machine
Planning of induction coil of high frequency quenching machine:
The planning of the induction coil is based on:
(1) The shape and scale of the workpiece;
(2) Technical requirements for heat treatment;
(3) The accuracy of the quenching machine tool;
(4) Bus bar distance, etc.
The planning content includes the shape, size, number of turns (single turn or multiple turns) of the induction coil, the gap between the induction coil and the workpiece, the size and connection method of the manifold, and the cooling method.
1. Planning of the gap between the induction coil and the workpiece
The size of the gap directly affects the power factor of the induction coil. The gap is small, the power factor is high, the current penetration depth is shallow, and the heating speed is fast.
When choosing a gap, consider:
(1) The accuracy of the quenching machine tool should be larger when the accuracy is poor. Because the gap is too small, the workpiece is easy to hit the induction coil and arc, resulting in damage to the induction coil and the workpiece is invalid.
(2) Equipment power: when the equipment power is large, it can be appropriately larger to facilitate operation.
(3) The depth of the hardened layer; when the depth of the hardened layer is large, it should be larger to extend the heating time and increase the heat penetration depth.
Usually, the gap between the induction coil of high-frequency induction heating and the workpiece is about 1 to 2 mm.
2. Induction coil height
When the long shaft is partially heated at one time, the height of the induction coil is: H=L+(8-10mm), where L is the length of the hardened zone (mm).
When the short-axis parts are partially heated at one time, the height of the induction coil is: H=L-2a, where a is the gap between the induction coil and the workpiece.
If the hardened area of the shaft-shaped part is long, a multi-turn inductor or moving continuous heating can be used.
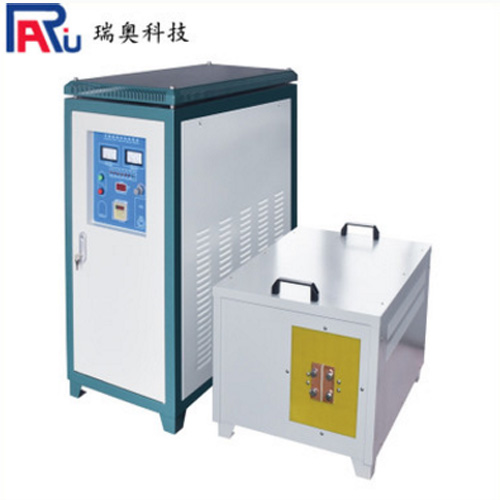